作刀工程
日本刀はその名のとおり日本固有のもので、世界の鉄工芸品でも最高峰に位置付けられています。日本刀は武器としてその要件を満たすよう、制作には工夫と努力が積み重ねられてきました。
日本刀の素材
日本刀の素材は、日本古来の製鉄技術であるたたらによって生産されます。
このたたらによって生産された広義の鉄は、以下の3種類からなる鉧 (けら)という塊です。これを破砕・選鋼して、それぞれ炭素量によって以下のように分類します。
狭義の鉄(てつ) ・・・ 炭素量0.0~0.03%のもの。加熱せずとも叩けば伸びるもの。
鋼(はがね) ・・・ 炭素量0.03~1.7%のもの。加熱して、叩けば伸びるもの。
銑(ずく) ・・・ 炭素量1.7%以上のもの。加熱しても何をしても伸びないもの。
この「鋼」に分類されるもののうち、特に破面が均質で良好なものを「玉鋼(たまはがね)」といい、これはそのまま刀剣の素材になります。
一方で、銑は炭素量が多いのでこれを取り除き(脱炭)、鉄は逆に炭素を吸収(吸炭)させ、鋼の炭素量に調節して使用します。
日本刀の制作工程
日本刀の制作方法は、時代・流派・個人によって多少違ってきますが、ここでは玉鋼による一般的な制作工程について説明します。
1.水へし・小割り
玉鋼を熱して厚さ5mm程度に打ち延ばし、次にこれを2~2.5cm四方に小割りして、その中から良質な部分を3~4kg選び出し、直接の材料とします。
2.積沸し
小割りにされた素材をテコに積み上げて、ホド(炉)で熱します。この過程で素材が充分に沸かされ(=熱せられ)一つの塊となります。
3.鍛錬(たんれん)・皮鉄(かわがね)造り
炭素の含有量を調整し不純物を除去するために、鍛錬を行います。鍛錬の方法は、充分沸かされた素材を平たく打ち延ばし、さらに折り返して2枚に重ねます。この作業を約15回程度行いますが、特にこの工程の前半を下鍛(したぎた)え、後半を上鍛(あげぎた)えといいます。
鍛錬によって、皮鉄(=軟らかい心鉄をくるむ、硬い鉄のこと)が作られます。15回ほどの折り返し鍛錬の結果、自乗計算すると約33,000枚の層となります。日本刀が強靭である理由のひとつがここにあります。
4.心鉄(しんがね)造り・組み合わせ
皮鉄造りに前後して、心鉄を作ります。日本刀は「折れず、曲がらず、よく切れる」という3つの条件を追求したものですが、切れるためと曲がらないためには鋼は硬くなければならないし、逆に、折れないためには鋼は軟らかくなくてはなりません。この矛盾を解決したのが、炭素量が少なくて軟らかい心鉄を炭素量が高くて硬い皮鉄でくるむという方法です。これは日本刀制作の大きな特徴です。
くるむ方法は甲伏(こうぶ)せ、本三枚(ほんさんまい)、四方詰(しほうづめ)など多くの種類がありますが、これは時代・流派・個人によって異なります。
5.素延(すの)べ・火造(ひづく)り
皮鉄と心鉄の組み合わせが終わると、これを熱して平たい棒状に打ち延ばします。これを素延べといいます。
素延べが終わると、小槌(こづち)で叩きながら日本刀の造り込みの作法に従って形状を整え、さらにセンスキ鑢(やすり)で肉置きを整えます。これが火造りです。
6.土置き(土取り)・焼き入れ
耐火性の粘土に木炭の細粉、砥石の細粉を混ぜて焼刃土(やきばつち)を作ります。これを刃文の種類に従って、土塗りをしていきます。焼きの入る部分は薄く、他は厚く塗り、これを約800度くらいに熱して、頃合いを見て急冷します。
7.仕上げ・銘(めい)切り
焼き入れが終わると、曲がり、反りなどを直して荒砥ぎをします。
最後に、刀身に疵(きず)や割れができていないことを確認し、中心(なかご)の鑢仕立てを行い、目釘孔(めくぎあな)を入れ、最後に作者の銘を入れます。
日本刀は、武器として求められた「折れず、曲がらず、よく切れる」という機能に含まれる矛盾を、様々な工夫により一振りの刀として作りあげてきました。そして、そのような実用から産まれた美に日本刀の魅力があるのです。また、武器でなくなった今日でも、日本刀が伝統工芸品である限り、この制作の過程は忠実に守られていくべきでしょう。
日本刀の研磨
日本刀の研磨技術は、日本刀の完成と共に高度な進展をとげてきました。鳥羽上皇の時代には、既に専門の研ぎ師の存在が確認されています。その後も研磨技術に磨きがかけられていき、明治になって名人とうたわれた本阿弥平十郎成重が現れ、高度な伝統技術にさらに美的感覚が加味され、今日見る美術刀剣研磨の技法が確立されました。
研磨の仕事は、日本刀がもつ独特の曲線美、鍛えぬかれた地鉄(じがね)、そして華麗な刃文、これらの美しさを発揮し、日本刀がもつ優雅さと尊厳を導き出すところにあります。
1.下地研(したじと)ぎ
日本刀の研磨は大きく分けると、下地研ぎと仕上研(しあげと)ぎに分けることができます。
下地研ぎとは、刀剣の姿や形を整える基本的な仕事で、普通は6種類の砥石が用いられます。それらの砥石の種類を目の荒い順から並べると、次のようになります。
・ 伊予砥(いよど)・・・愛媛県松山から産出。約400バン(「バン」は目の荒さを表します)
・ 備水砥(びんすいど)・・・熊本県天草から産出。約400バン
・ 改正砥(かいせいど)・・・山形県から産出。約600バン
・ 名倉砥(なぐらど)・・・愛知県南設楽郡(しだらぐん)より産出。約800バンから1200バン
・ 細名倉砥(こまなぐらど)・・・産出地、名倉と同じ。約1500バンから2000バン
・ 内曇砥(うちぐもりど)・・・内曇砥には刃の部分を研ぐ内曇刃砥(はと)と地の部分を研ぐ内曇地砥(じと)の2種類があり、ともに京都から産出し、約4000バンから6000バン。
2.仕上研ぎ
下地研ぎが終わると、次に仕上研ぎに移ります。これには刃文の部分を研ぐ刃艶砥(はづやど)と地の部分を研ぐ地艶砥(じづやど)とがあり、刃艶砥は良質の内曇砥を薄く、小さく削り、裏に吉野紙を膠(にかわ)や漆(うるし)で裏打ちして用います。
地艶砥は鳴滝砥を薄く割って用いますが、流派によっては指先でさらに1mm角に砕いて用い、これを砕(くだ)き地艶(じづや)と呼んでいます。
3.拭(ぬぐ)い
仕上研ぎが終わると、次に拭いの作業に移ります。拭いとは、刀身に光沢を与えるために行われるもので、普通は金肌拭(かなはだぬぐい)という方法が用いられます。これは、日本刀鍛錬のときにできる酸化鉄を長時間焼き、微粉末にしたものを丁子(ちょうじ)油と混ぜ、さらに吉野紙で十分こしたもので磨く方法です。
4.刃取(はど)り
次は刃取りです。刃取りとは、刃の部分を白く美しく仕上げる作業をいいます。これに用いる砥石は刃艶砥で、内曇砥の砥汁をつけて刃文の形にそって研磨します。この作業を「刃を拾う」とも表現します。
5.磨き
刃取りを終えると、次は磨きに移ります。磨きとは、刀の棟、鎬地を長さ15cmほどの細い丸い鉄製の棒で磨き上げることをいいます。黒い独特の光沢は、この作業によって生まれるものです。
6.なるめ
ほぼ最終的な仕事と言えるものに、帽子の「なるめ」があります。なるめとは帽子を研磨することで、まず横手筋(よこてすじ)をきめる(=仕上げる)ことから始まります。横手筋がきまると、次に最も良質な刃艶砥がはられたナルメ台を用いて、横手筋をくずさないよう注意して帽子を研ぎ上げます。
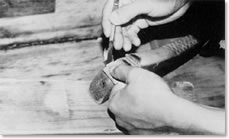
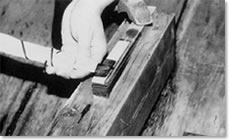
横手筋を決める 帽子のなるめ
7.化粧研ぎ
長い工程を経てきた研磨は、最後に化粧研ぎをもって終了します。中でも「化粧磨き」は、いわば研師のサインとも言うべきもので、磨き棒で帽子の棟に数本の線を磨き入れることを言います。
ここでは、日本刀ができるまでを、鍛錬、研磨について説明しました。しかし一口(ひとふり)の日本刀が完成するには、鞘師(さやし)、塗師(ぬりし)、柄巻師(つかまきし)、白金師、彫金師など、その道を極めた多くの職人の技術が必要となります。日本刀制作の大きな特徴は、これら全ての技術が結集して初めて一口の日本刀として完成するところにあると言えましょう。